超声自动检测技术在变径复合壳体中的应用········王飞 金翠娥 危荃 盛涛
超声自动检测技术在变径复合壳体中的应用
(1. 上海航天精密机械研究所,上海 201600;
2.上海复合材料科技有限公司,上海 201112)
关键词:超声 自动检测 复合壳体
WANG Fei1,JIN Cui’e1,Wei Quan1, Sheng Tao2
(1 Shanghai Spaceflight Precision Machinery Research Institute, Shanghai 201600, China)
(2 Shanghai Composite Technology Co.Ltd,Shanghai 201112, China)
Key words: Ultrasonic testing; Automatic detection;Composite shell
固体火箭发动机燃烧室一般采用壳体/绝热层/包覆层/推进剂的多界面结构形式,其中绝热层采用复合材料缠绕成型后与金属旋压胶接而成,在胶接过程中若存在壳体内部多余物清理不干净,绝热层与壳体配合不严,胶层内部气体未排净等情况,则容易导致粘接层产生脱粘缺陷,尤其当存在间隙型大面积脱粘缺陷时,往往会引起推进剂碎裂、燃面急剧增加进而导致燃烧室压力失控、发动机壳体烧穿等情况,严重时甚至会引起发动机爆炸等灾难性后果[1-3]。因此,对发动机燃烧室粘接界面的质量控制和检测显得尤为重要。
1 产品对象及检测需求
本文所涉及发动机燃烧室壳体为一带有锥形过渡段的小直径柱体结构,如图1所示。
上述产品在制造过程中,当钢壳体与绝热层胶接结束后需要对其胶接质量进行超声检测。目前采用的检测方法为超声纵波多次反射法,其检测原理是当超声纵波垂直穿过钢壳体与绝热层粘接面时,由于两者的声阻抗不同,声波在界面处会产生反射和透射,若不考虑超声波在耦合剂及钢壳体中的声衰减,则在钢壳体与绝热层界面处产生的一次反射回波的声压可简化成如下公式:
P1=P0T12T21R23
..............................(1)
......................................(2)
式中为入射声波声压,P0为耦合剂与钢壳体界面的透射系数,T12 、T21为钢壳体与粘接层界面反射系数,R23为钢的声阻抗,Z2为粘接层声阻抗。由公式(1)可知,第n次反射回波声压值只与反射系数R23有关,即Pn∝Rn23。当界面脱粘时lR23l~~1,超声反射回波声压(对应回波信号幅值)随反射次数的增加下降缓慢,当界面粘接良好时lR23l<1,超声反射回波声压随反射次数的增加而迅速下降[4-6]。上述这种差异在多次反射后可以明显区分,进而可实现壳体与绝热层这一界面粘接质量检测,图2和图3分别为脱粘部位和粘接完好部位不同A扫描波形图。
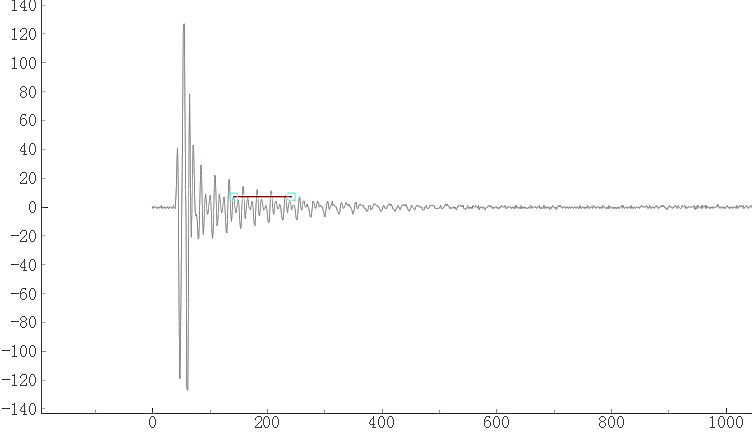
图3粘接完好部位A扫描波形图
由于原有的检测工艺方法的实施主要依靠人工手持探头采用直接接触法进行检测,检测过程中通过观察A扫描的多次反射波形进行判断,其方法受操作者的技术能力、检测经验、工作状态等人为因素的影响且检测结果无法直观显示和记录,使得缺陷评价难、结果可追溯性差,同时效率也难以满足批量化检测需求。因此为解决上述问题,本文针对上述变径壳体的产品结构特点、超声检测工艺方法原理及验收技术条件要求,设计开发了用于粘接层胶接质量检测的超声自动检测系统,通过采用机械扫查装置代替人工手动扫查,在提高检测效率的同时实现了粘接界面的C扫描图像化检测评价。
2 自动检测系统关键技术解决方案
2.1探头耦合及密封设计
由于本文所涉及的发动机燃烧室外部壳体材质为钢,为避免超声检测过程中耦合剂对钢壳体表面的腐蚀影响,超声自动检测系统设计时采用机油作为耦合剂。同时为确保探头与壳体表面耦合良好,在耦合方式上仍然采用直接接触法耦合,将探头耦合楔块加工成与壳体检测面贴合较好的弧形结构并在楔块上加工多个注油孔,采用局部喷油浸润耦合方式,从而保证探头有效接触和良好耦合。
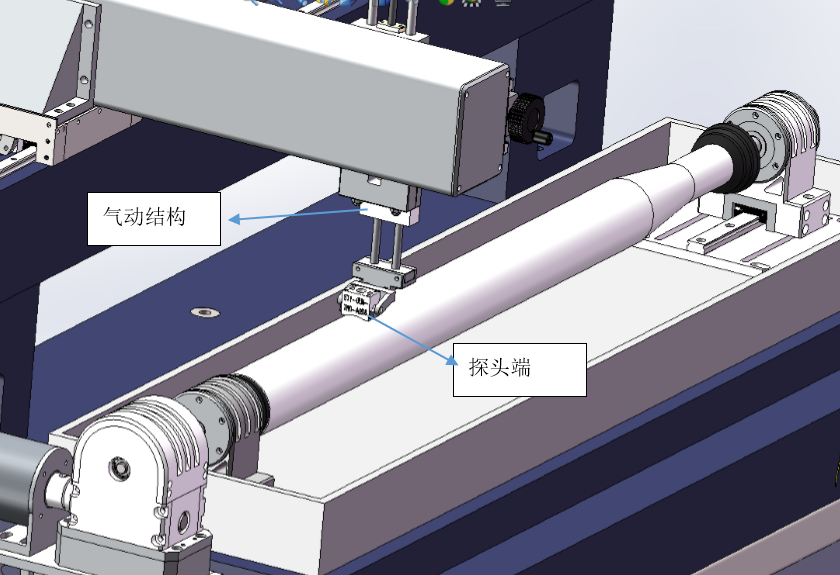
图4 探头结构示意图
与此同时,考虑到壳体与绝热层粘接界面的检测为过程工序检测,检测结束后绝热层内部还要进行包覆层及推进剂的装填,因此检测时不允许有机油渗漏到壳体内部。而该检测状态下壳体为中空结构且两端分别有约50mm长的纯金属端,金属端周向分布有少量通孔或槽。针对上述问题除机械扫查参数行程设置上有效避开两侧金属端检测区域外,同时在硬件上进行了优化设计:1)工件夹持装置采用顶针结构,顶针端采用非金属材料加工成圆锥状,在实现快速夹持、端部内撑密封的情况下不会对工件表面造成机械损伤;2)针对金属端通孔或槽部位采用具有一定宽度的弹性橡胶密封圈包裹,可以有效防止部分剩余的耦合机油从开口的孔、槽部位渗入。此外在工件下方设有耦合液收集槽和油泵循环系统,可将收集的耦合液通过泵输送到探头楔块端。
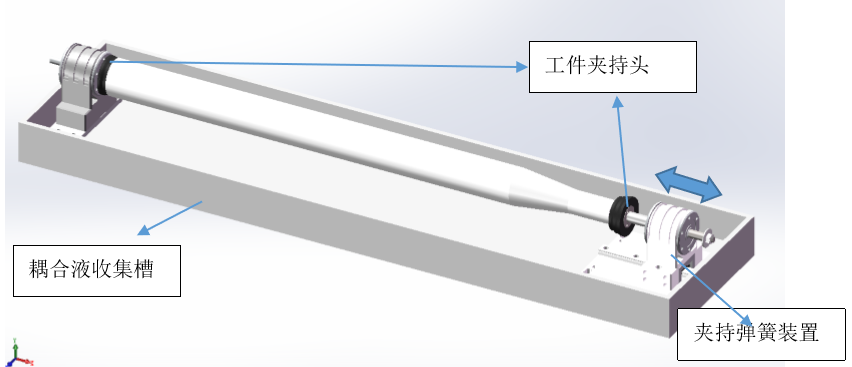
2.2 不同直径端探头自适应扫查设计
超声纵波多次反射法在检测过程中须确保入射声束始终与待检粘接面垂直,对于本文所涉及的变径壳体检测而言,机械扫查过程中需兼顾不同大小直径端以及中间锥形过渡段的探头声束入射方向的自适应调整问题。在分别针对大直径和小直径端进行检测时,探头始终位于壳体正上方,其直径变化对声束垂直入射影响较小,但考虑到工艺所要求的壳体与绝热层粘接面最小可检脱粘缺陷为Φ5mm,因此为保证检测效果同时降低大尺寸探头接触耦合及声束扩散所带来的影响,最终选择晶片有效直径为Φ3mm的小晶片探头进行检测。对于锥形过渡段的探头自适应问题,系统设计过程中将探头夹持端设计成可上下运动以及楔块可以转动调节的两个自由度,检测过渡段时分别通过探头夹持装置的气动下压力确保探头与检测面始终贴合,同时利用探头夹持端的楔块自由转动可确保直筒和锥形段的有效过渡,图4、图6
。
图6
变径壳体超声自动检测系统结构示意图
3试验与应用验证
为进一步验证超声C扫描检测系统的检测灵敏度、机械扫查装置的稳定性,设计制作了2件对比试块并开展了检测工艺验证试验。其中试块制作均选用复合壳体工件实物,采用机械切割方式将壳体中间半个柱体切除后再通过钻孔加工方式从绝热层加工不同孔径的平底孔,孔深为相应部位绝热层的厚度,从而确保所加工的平底孔的孔底部即为壳体与绝热层的粘接面。试块1为单一直径壳体,共加工了7 个人工缺陷,孔径尺寸分别为:3、5、7、13、15、20mm;试块2为变径壳体共加工了10个缺陷,其中大直径端孔径尺寸分别20、17、14、12.5、9.5、7、5mm,小直径端孔径尺寸分别为10、7、5mm。
扫描成像图
扫描成像图
4 结束语
本文针对某固体火箭发动机燃烧室壳体与绝热层粘接结构批量化检测需求,研制了研制了具备快速装夹与自适应扫查的超声自动检测系统,通过方案优化设计有效兼顾了壳体检测过程中的表面锈蚀与内腔渗油防护、壳体不同直径端及锥形过渡段的自适应检测问题,经对比试块工艺试验及工程应用验证,表明该系统检测灵敏度、稳定性均能够满足实际应用需求,对于类似管件产品结构检测具体广泛的工程推广应用价值。
参考文献
[1] 艾春安,刘瑜,赵文才,等.固体火箭发动机结构粘接质量的声-超声检测[J].无损检,2009,31(12):974-976.
[2] AI Chun-An, LIU Yu, ZHAO Wen-Cai, et al. Acousto-Ultrasonic Testing for Bond Quality in Solid Rocket Motor Struetuer[J]. Non Destructive Testing, 2009,31(12):974-976.
[3] 郭洪涛,曹付齐. 固体火箭发动机装药界面胶接质量超声波检测[J].航空兵器,2006,6:49-52.
[4] GUO Hong-tao, CAO Fu-qi. Ultrasonic Testing of the Interface Bonding Quality of Solid Rocket Motor Charge[J].Aero Weaponry, 2006,6:49-52.
[5] 赵慧蓉.固体火箭发动机喷管粘接界面的超声检测[J].固体火箭技术,2000,23(2):74-78.
[6] ZHAO Hui-rong. Ultrasonic Detection of Bonded Interfaces for Solid Motor Nozzles[J]. Journal of Solid Rocket Technology, ,2000,23(2):74-78.
2019中国超声检测大会论文作者信息表
姓名 | 王飞 | 性别 | 男 |
手机 | 18116239316 | 电子信箱 | wf0420@163.com |
通信地址 | 上海市松江区贵德路76号 | 邮政编码 | 201600 |
工作单位 | 上海航天精密机械研究所 | ||
论文交流形式 | *提交全文口头报告;R提交全文张贴报告;*提交摘要口头报告。 | ||
备注 |
- 上一篇:暂无
- 下一篇:暂无